Machining guidelines Chapter 4
- Henk Lourens
- Aug 31, 2017
- 2 min read
Tempering
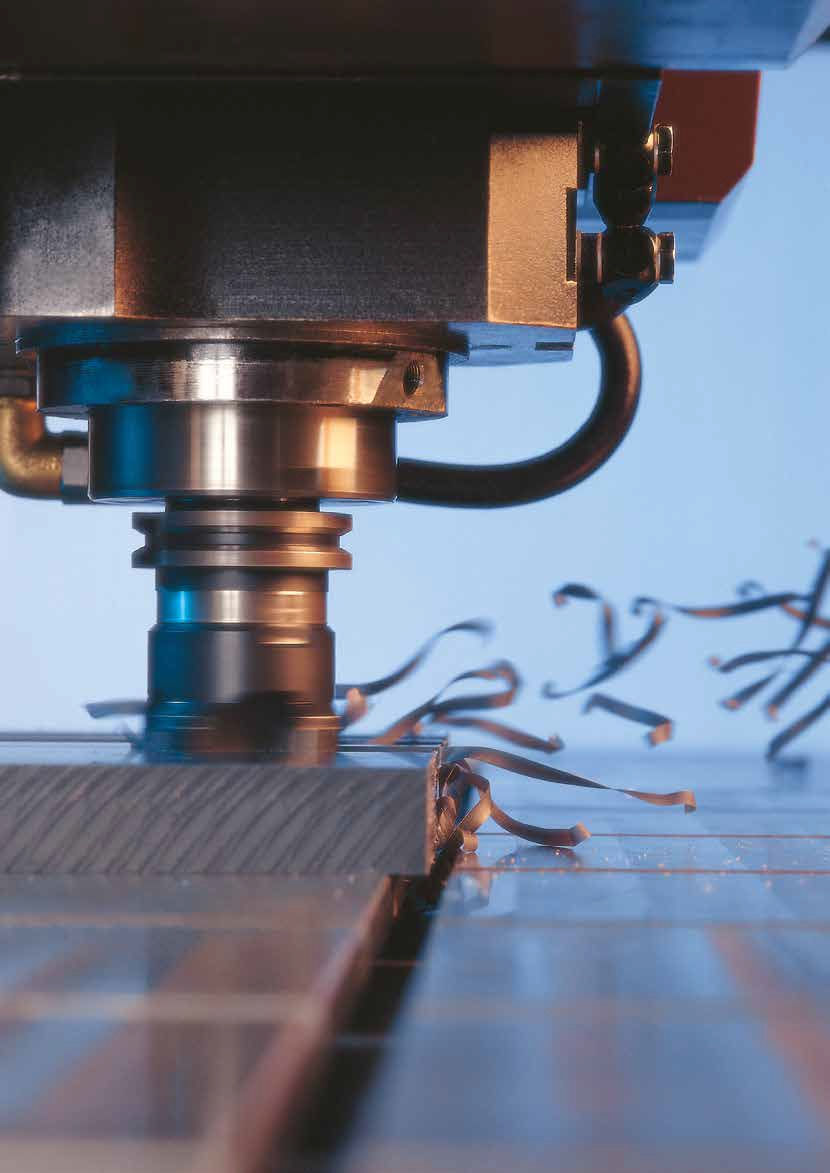
The tempering process is defined as the heat treatment of parts or semi-finished products in order to
largely reduce residual stresses from the manufacturing or production process
increase the crystallinity and thereby to improve the mechanical characteristics of the material
prevent warping and dimensional changes during or after machining
improve the permanent dimensional stability
Usually semi-finished products and parts are tempered in an oven using hot circulating air. Hot oil baths using a paraffin or silicone oil base are also commonly used. The process is based on a uniform scheme regardless of the heat transfer medium used. The products are slowly and evenly heated in a heating cabinet (in the media) and brought to the material-specific tempering temperature. Once this is achieved the products are kept at this temperature for several hours. The complete warming through of the products is essential and crucial for tempering to be a success. The holding period required is dependent on the product dimensions and shape as well as its mass and is set based on these parameters. On completion of the holding period ensure that the tempered material cools to room temperature slowly, draught-free and under control. This will ensure the formation of a highly crystalline structure in the material and that only minimum residual stresses result from uneven heat losses during the cooling phase.
The temperature range for common technical plastics is usually between 130 °C and 170 °C. Some materials (such as the high-temperature plastics) require higher temperatures. In special cases technical plastics can also be tempered at higher temperatures.
SMXLL
However, specific process conditions must be complied with and it must be ensured that the maximum temperature is always 30 to 40 °C below the melting point. The general specification of the required heating, holding and cooling times is only possible to a very limited extent. The dependencies on product dimensions, shape and mass of the goods to be tempered are very large. For example, a large mass requires a significantly higher quantity of heat and heating period to reach full and uniform heating than a small mass. It also needs a significantly longer cooling time as the quantity of heat adsorbed is released at a slow rate due to the large mass. The following diagram clearly shows these differences using newly cast solid Nylon rods as an example.
It is evident that a solid rod with Ø 100 is cooled enough to be tempered one day after demoulding. However, a solid rod with Ø 700 mm needs at least four days until it is cooled down enough for the tempering process to begin.
But also the product form has a significant influence on the tempering times. Pipes are for example completely warmed faster than solid rods because they offer a greater surface area to heat absorption due to inner and outer diameter. Accordingly these cool down faster again after tempering than solid bars.
If parts are to be intermediately tempered during manufacturing, in addition to the above parameters also the geometric conditions of the construction part as well as the existing wall thicknesses and their distribution on the workpiece are to be considered.